- Overview
- High Performance Reamers
-
Core drill,CounterBoring
and Deburring Tools - Machine Reamers
- Hand and Taper Reamers
- Special designs
Products > Beck > Overview
AUGUST BECK
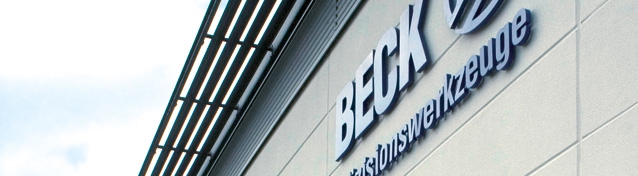
Building on its many years of experience in the field of fine machining of bores, BECK has specialised in recent years in the production of
multi-bladed monoblock reamers and counterboring tools and has earned itself an excellent reputation in this sector.
The typical Swabian virtues such as inventiveness, industriousness, economy and the perseverance to unwaveringly pursue the goals
set have made a major contribution to this. With some 160 employees, a range of high-quality precision tools is produced on the latest automated production facilities at the
company's headquarters in Winterlingen.
These includes:
- 1) High-performance reamers with internal coolant supply of carbide and Cermet with PCD and CBN cutting edges for high machining values
- 2) Reamers, counterboring tools and core drills to DIN and to works standards
of HSS and carbide - 3) Special tools designed individually for the customers' machining processes.
Products > Beck>High Performance Reamers
High Performance Reamers
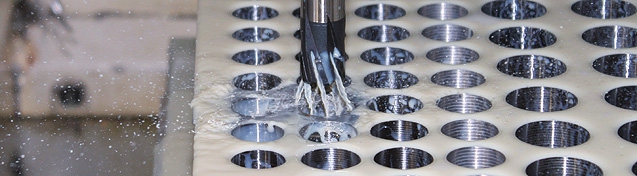
High-performance reamers are equipped with internal coolant channels which transport the cooling lubricant directly to the blades,guaranteeing optimum lubrication and cooling of the blades and allowing the highest cutting data to be achieved,and hence significantly increasing productivity. The special design paired with modern cutting materials and coatings give the tools from this reamer group a particularly high performance. The whole diameter range from 3 to 40 mm is covered by solid carbide or solid Cermet reamers and series with soldered blades.
Main fields of application and product features:
- 1) on machining centres and special machines
- 2) For high quantities
- 3) For close tolerances
- 4) For the highest surface qualities
- 5) Broad choice of cutting materials and coatings
- 6) Special designs, such as for HPC, stainless steel, hard machining, aluminium

High machining data demand high process reliability. These primary demands on a reamer in the modern production process regularly present
many users with great problems, because only tool solutions that meet these demands offer the preconditions for an inexpensive product that
can be produced in high quantities and with a consistently high quality.
In the field of fixed reamers, a design was therefore integrated which allows enormous machining speeds and at the same time close tolerances and the
highest surface qualities in the sense of high-performance cutting. The tool concept of the HPC version is characterised by its wide range
of application possibilities. At the same time, machining qualities are achieved comparable with those produced by grinding or honing.
An important expansion to this range of HPC Cermet reamers is the expandable variant. It combines the advantages of the solid tool
with those of adjustability. The adjustment mechanism can easily absorb the enormous loads of HPC machining. By contrast with the solid variant,
the tools are fitted with soldered Cermet blades. The adjustment range is approx. 0.03 mm above the nominal diameter.
The main fields of application of the expandable variant are the compensation of wear-related reductions in diameter and the
allowance for material-specific and clamping-related influences on the machining diameter.
MR REAMERS :
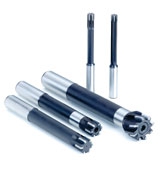
With the newly developed high-performance reamers from the MR series 01, 02 and 03, BECK is providing the first standardised
system for multi-bladed reamers. The reduced number of variants in these series covers a large number of possible
applications in fine machining with significant rationalisation effects.
The MR reamers in this programme are available as fixed, expandable or finely adjustable variants that have interchangeable
primary dimensions and in this way cover a wide spectrum of applications. As straight or left-hand fluted versions they are
suitable for through bores or blind bores and can be designed with suitable cutting materials, coatings and cutting leads to suit the material of the part.
Advantages :
Due to the compatibility between the series, it is possible to straightforwardly change to the optimum system reamer for the specific case if general conditions change in production,for example different quantities or bore tolerances. In this way the flexibility of the MR system guarantees the most cost-effective solution.
- 1)Three series with the same dimensions
- 2) All versions with internal cooling
- 3) Direct mounting in expanding, shrinking and high-precision chucks
- 4) A variety of cutting materials cover the whole spectrum of materials to be machined
- 5) Variants for through bores and blind bores
- 6) Flexibility in use
- Interesting alternative to solid carbide tools
- Flexible system thanks to possibility of changing to expandable or finely adjustable versions
Design :
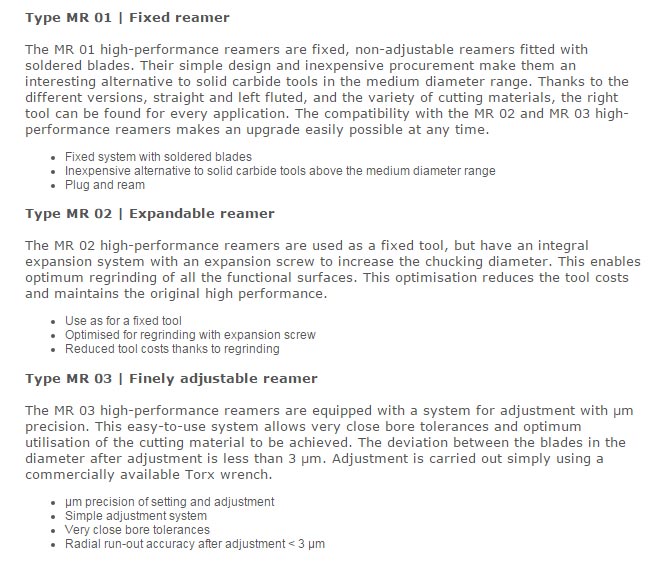
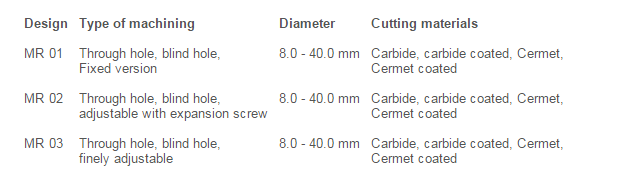
RR01 REAMERS:
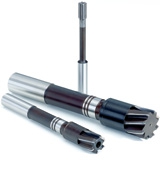
In order to meet these demands, Beck has developed the RR 01 product family.The extensive range available from stock offers through bore and blind bore variants as well as an expandable version for through bores to quickly meet customers' needs.
Advantages :
The main field of application of our RR 01 reamers lies in the machining of steel and cast iron (GGG50). The outstanding feature of this product range is the optimum guidance of the cooling lubricant to prevent thermal shock at the start of material cutting. The extremely unequal spacing in relation to the geometry is also a major determining factor for the good machining results of this product range, and due to the fact that the standard sizes in the diameter range from 4-40 mm are available from stock, our RR 01 reamers can be delivered without long waiting times. From the economic point of view, too, the RR 01 Series is an interesting variant to tools previously used, as the RR 01 can be conditioned by our regrinding service and is then inexpensively ready for use again.
Design :
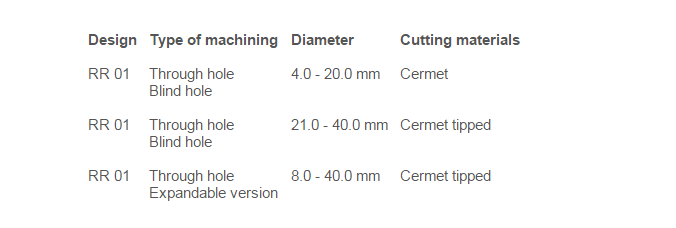
VR01 REAMERS:
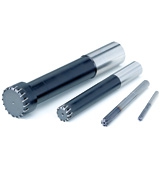
A crucial criterion for the performance of multi-bladed reamers is the number of blades. A design limit on the number of blades is defined by both the
diameter of the reamer and the space required for blades and chip spaces.The VR01 multi-tooth reamers push back the existing limits by eliminating
the chip spaces and creating room for more blades. At the same time effective coolant supply directly to the blades is still ensured.
The coolant is supplied via a streamlined duct that is formed at the periphery between the blades and the
wall of the bore and therefore also ensures cooling and lubrication of the blades for high speed machining.
Advantages :
The blades on the reamer body can be easily replaced and reconditioned several times. At the same time, the additional blades on the VR 01 create several
other positive effects for machining. The machining time is drastically reduced,the tool lives are increased and the bore quality, in particular the circularity of
the bore, is improved. The shape of the tool, which is defined by the design, ensures the chip is intentionally discharged forward. In addition,
the coolant also ensures reliable chip transport forward.The chips therefore do not come into contact with the part of the bore already reamed.
The strengths of the VR 01 multi-tooth reamer include the machining of steel and castings. Reaming using the multi-tooth reamer is so effective that, for instance,
honing during fine machining of bores for hydraulic components is often no longer required.
Design :
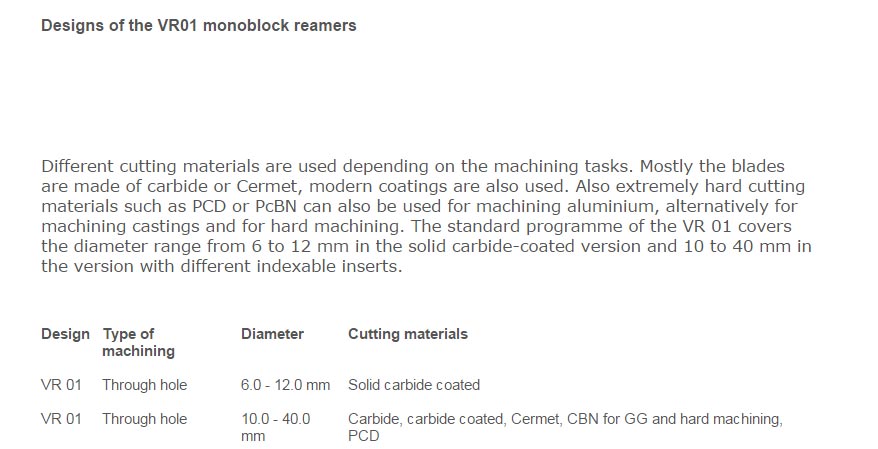
HNC REAMERS:
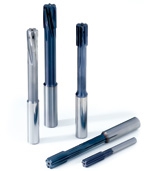
This series particularly suitable for high-performance machining impresses with its high performance,the high cutting data that can be achieved and the resulting high productivity.An outstanding feature is the special design which allows a selective coolant supply directly to the blade.The production from solid carbide with various high-strength coatings makes this tool series an interesting solution for the machining of a wide range of materials..
Advantages :
In its preferred field of application of steel machining, the HNC reamer is a real "work wonder".But in the machining of aluminium, CFRP, GFRP, stainless steel or for hard machining,The HNC reamers with their specially developed blade geometry provide outstanding work results.Furthermore, our HNC reamers in the diameter range between 3 and 20 mm are a particularly cost-effective alternative to other methods of machining. The HNC reamers are designed with extremely unequal spacing in their geometry and are available in many fitting diameters from stock.
Design :
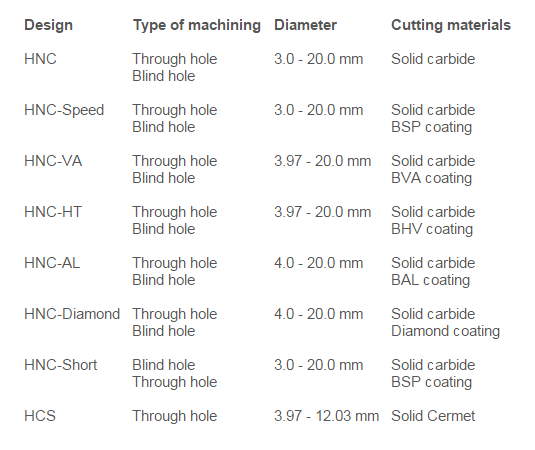

In order to counter the rising tool costs, BECK has developed a modular tool system that offers a high degree of flexibility as the tool holders can be fitted with different
reaming heads via defined interfaces.
The advantage here lies in the fact that only one holder adapted to the machine interface is required for different
machining operation and the optimum reaming heads can be selected with respect to cutting material, coating and blade geometry to suit the material to be machined.
Short tool change times, generally without remeasuring, make this type of tool attractive for medium and large lot sizes as the change can be carried out directly at
the machine.
The basic holders are so stable and designed with µ-precision so that the additional interface compared with monoblock tools presents no limitations.
A further positive aspect for replaceable head tools is the high savings potential with respect to the material costs, particularly with large diameter.
XR REPLACEABLE HEAD REAMERS
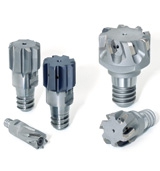
Precision and stability are crucial for a modern, high-performance replaceable head system for reaming.The new XR replaceable head reamers from BECK satisfy all these demands to the letter.The connection is designed such that the best possible stability and rigidity are achieved by a taper and a face connection. The special design and manufacture of the thread and taper-face section guarantee the highly precise radial run-out accuracy .
Advantages :
Thanks to the simple and safe handling, the reaming heads can be replaced in the machine tool quickly and easily. That saves setup costs. The range of XR
replaceable head reamers covers three different series of replaceable heads in the diameter range from 8 to 40 mm for through holes and blind holes.
The most important elements of the new connection are the taper and plane face.The exact interplay of these elements ensures maximum stability and rigidity.
Taper and plane face are complemented by a threaded journal directly adjoining the taper and connected to the taper in one piece. These three characteristics
coordinated perfectly with one another ensure the highest changeover accuracy, high clamping force and very simple handling at the new connection.
Modern production facilities allow plane face and taper to be manufactured with the highest accuracy,
and hence to reliably achieve a radial run-out of ≤ 5 µm. The high stability of the system results from the pretension of the taper.
When tightening completely, the taper expands slightly in the holder and the plane face has a perfect contact.
Design :
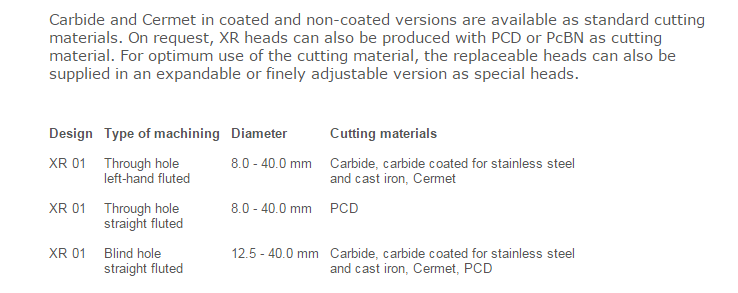
XR HOLDERS
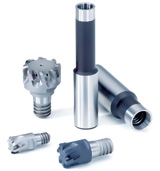
The advantage of the XR replaceable head system derives to a great extent from the fact that only a small number of holders have to be kept is stock, for example different lengths, leading to a significant cost saving. The heads can be selected with respect to cutting material, coating and blade geometry to suit the material to be machined. The exact interplay of plane face and taper supplemented by a threaded journal creates a high-precision interface with maximum stability and rigidity.
Advantages :
- XR holders in different lengths available as standard
- Diameter ranges from 8 mm to 40 mm can be covered with just 6 connection sizes
- Maximum changing precision, high clamping force and very simple handling
Design :
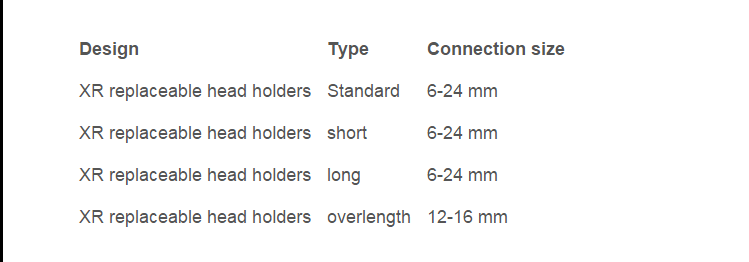
Products > Beck> Machine reamers-reaming without internal cooling
MACHINE REAMERS-REAMERS WITHOUT INTERNAL COOLING
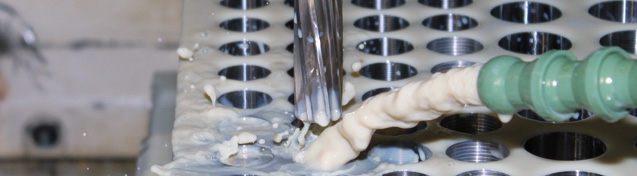
With its broad range of standardised reamers to DIN, BECK offers a good complement to the high-performance reamers with internal cooling. With small lot sizes
or when machining on older machines without internal cooling lubricant supply, the advantages of the high cutting data of the high-performance reamers cannot
be utilised, so that an inexpensive DIN reamer can be the more profitable solution for these machining operations. A further benefit of the DIN versions is the
particularly high availability from stock, so that a reaming solution can be offered even at very short notice.
Apart from the DIN versions, BECK also offers NC
reamers similar to DIN. On these reamers, certain features have been modified, such as the chucking diameter to full diameter, in order that standard expanding
chucks or shrink chucks can be used. Miniature reamers above 0.6 mm diameter complete the BECK product range. Taper reamers and hand reamers round the
product range for reaming without internal cooling off.
MACHINE REAMERS OF SOLID CARBIDE:
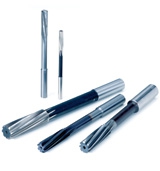
Reamers to DIN and DIN-like versions of carbide without inner cooling lubricant supply are suitable for a wide range of operations and offer a very wide spectrum of applications. The high hardness and good heat resistance of carbide allow higher machining data and longer tool lives than for reamers of HSS-E.
Advantages :
- Suitable for small to medium-sized batches
- Inexpensive alternative as DIN reamer
- High availability from stock
Design :
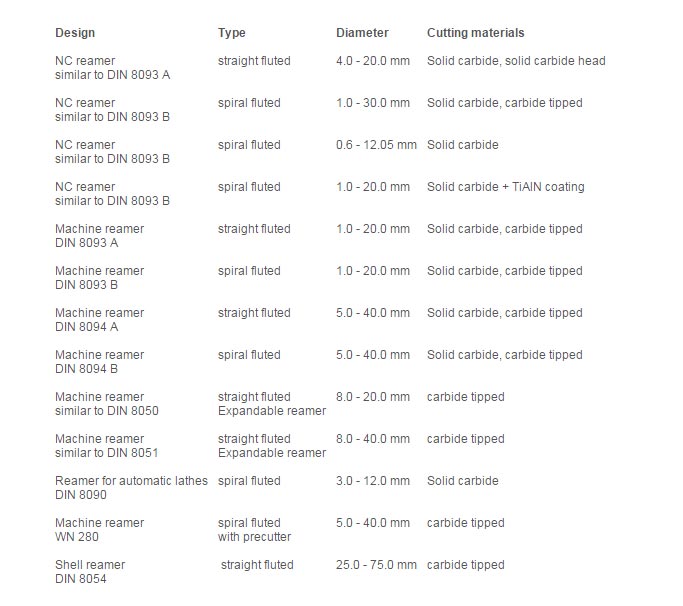
MACHINE REAMERS OF HSS:
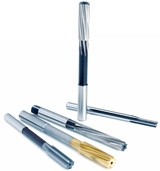
Reamers to DIN and DIN-like versions of HSS-E without internal cooling lubricant supply are suitable for a wide range of operations and offer a very wide spectrum of applications. Machine reamers of HSS-E are a particularly inexpensive variant for the production of precision bores. They are characterised by their ease of handling and can be used even under difficult machine and cutting conditions.
Advantages :
- Suitable for small to medium-sized batches
- Inexpensive alternative as DIN reamer
- High availability from stock
- HSS-E as inexpensive variant for reaming with low cutting data
- Use only of European high-performance steel
- Consistently high quality thanks to continuous material analyses and hardening process at Beck
- Holders for shell reamers also available from stock
Design :
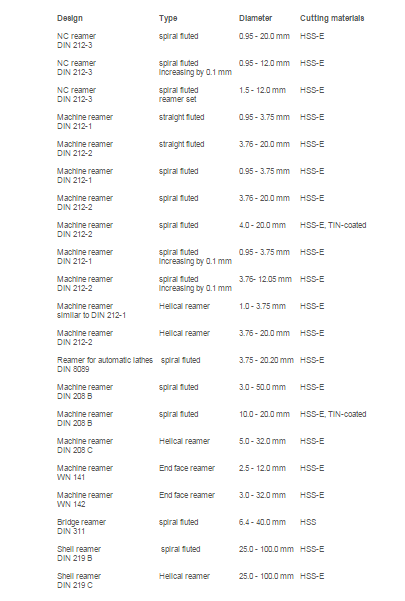
Products > Beck> Core drilling, counterboring, deburring, countersinking
CORE DRILLLING, COUNTERBORING, DEBURRING, COUNTERSINKING
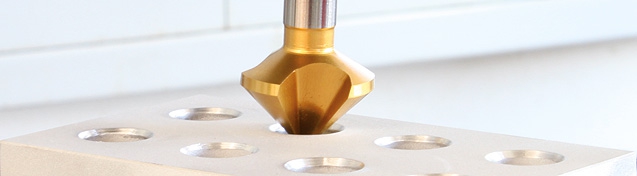
Core drilling, counterboring, deburring, countersinking tools complete the product range and form a comprehensive complement for bore machining. Countersinking operations are performed on practically all parts which have to be cut. Countersinking and counterboring tools are required in particular for flush screw connections. The spectrum extends from simple deburring tools right up to countersinks with highly wear-resistant coating.
Main fields of application and product features
- For flush and precise screw connections
- For core drilling before reaming
- HSS core drills as an inexpensive alternative to drilling tools with intermediate sizes
CORE DRILLS OF HSS:
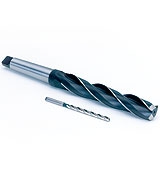
HSS boring tools are used to create the necessary initial size of a bore for the subsequent reaming. They are characterised by their simple handling. More important, however, is the preparation of the diameter for the subsequent reaming operation. This eliminates the need for expensive drilling tools with intermediate diameters.
Advantages :
Achievement of long tool lives through production in chip space ground quality Consistently high steel quality thanks to continuous material analyses and in-house hardening plant
Design :
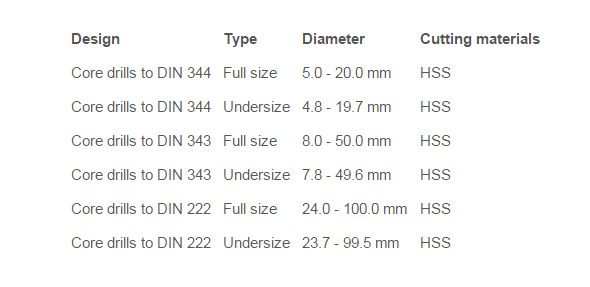
COUNTER-SINKS:
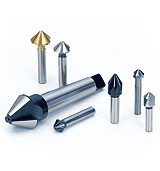
With its HSS countersinking tools in uncoated and uncoated variants and of solid carbide, BECK can offer the right tool for every application. With countersinking tools, coatings serve less to increase the machining speed than to provide a significant extension of the tool life.
Advantages :
The blades of countersinks are radially relieved. The relieve surface supports the tool in the bore. But countersinks from BECK are characterised by far more details. The chip spaces are finely ground and extra large so that the machining volume produced can be reliably discharged. In addition, the countersinks from BECK have an optimised cutting geometry that makes even the machining of long-chipping materials (e.g. stainless steel) a reliable process. Continuous material analyses and the in-house hardening process ensure a consistently high steel quality.
Design :
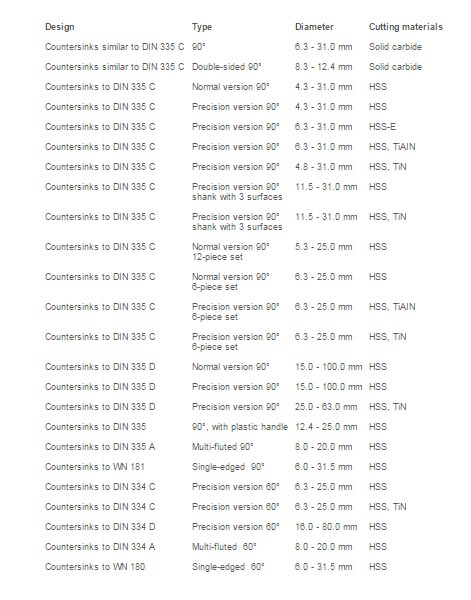
COUNTER-BORES:
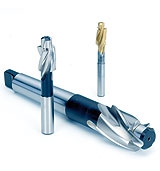
Counterbores are used to produce recesses with a smooth surface in the bores, e.g. head and shank recesses for cylinder head screws or smooth outer faces. The counterboring angle is 180°. There are 3 versions: for fine through bore, for medium through bore and for tapping bore.
Advantages :
All versions are supplied with ground chip space ->maximum increase in the tool life Counterbores with TiN coating are available for wear-resistant materials Top quality thanks to continuous material analyses and hardening process at Beck
Design :
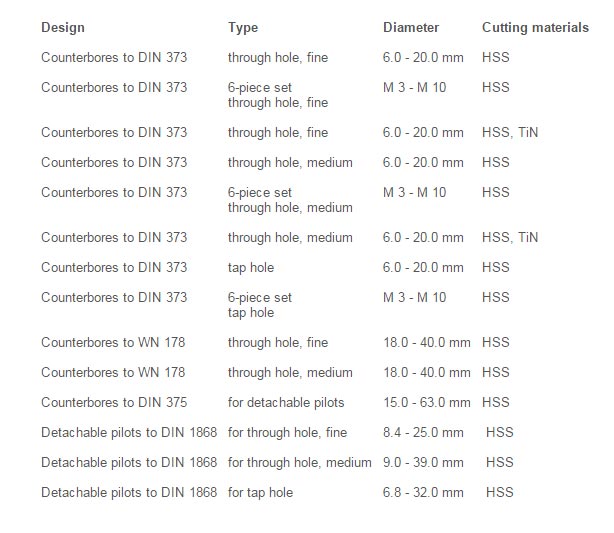
Products > Beck> Hand and taper reamers for manual bore machining
HAND AND TAPER REAMERS FOR MANUAL BORING
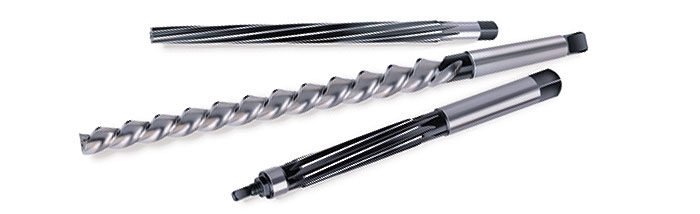
The manual machining of bores with difficult access or tapered transitions requires tools that are easy to adapt to the respective machining situations. Despite the manual machining operation, the use of BECK hand or taper reamers enables high surface qualities and good machining values to be achieved. Hand and taper reamers are manufactured from high-quality HSS steel.
HAND REAMERS:
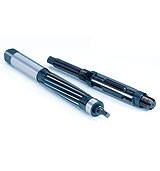
Hand reamers are frequently the best choice for repair applications. The cylindrical shank with square drive allows a bore to be post-reamed using a tap wrench.
But these tools are often also the only alternative at points inaccessible to machine tools. Hand reamers have a very flat and long cutting lead
so that the start of bore cutting is easier.
BECK hand reamers should not be used on machine tools as this cutting lead form can lead to dimensional and surface problems even at low spindle speeds.
Advantages :
Remachining during assembly or repair. For small to medium-sized batches. High availability from stock
Design :
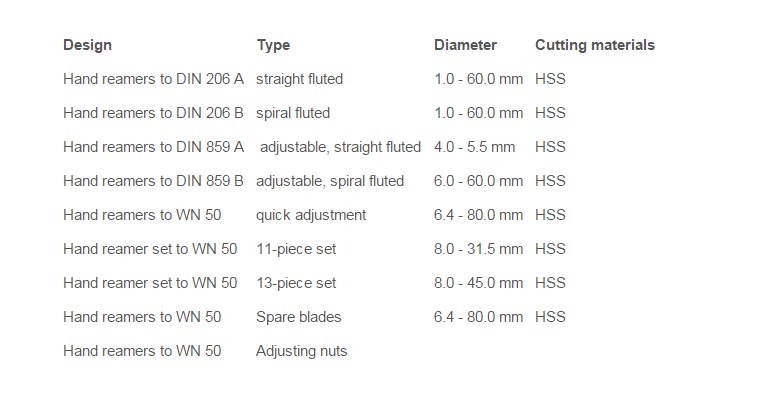
TAPER REAMERS:
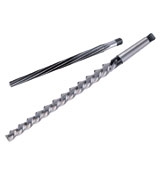
Taper fits which are generally subjected to high mechanical loads can be easily and effectively produced using taper reamers. The HSS/HSS-E cutting material offers the best preconditions for this. Its range of properties is a very good match for this shell cutting machining process which from the point of view of the cutting material demands a high ductility rather than a high hardness. The highest surface qualities are achieved with BECK taper reamers.
Design :
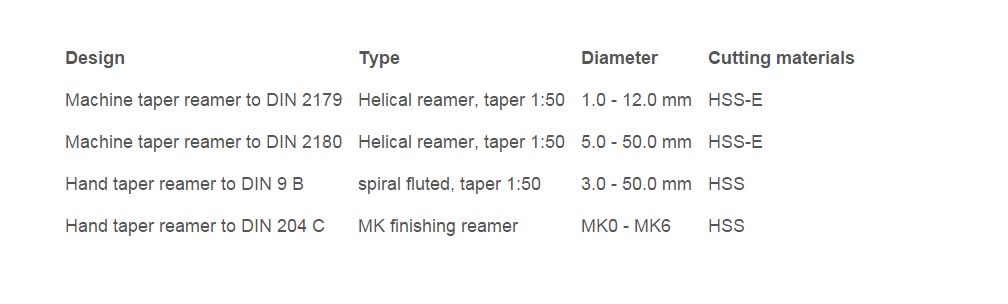
Products > Beck> SPECIAL TOOLS FROM BECK
SPECIAL TOOLS FROM BECK
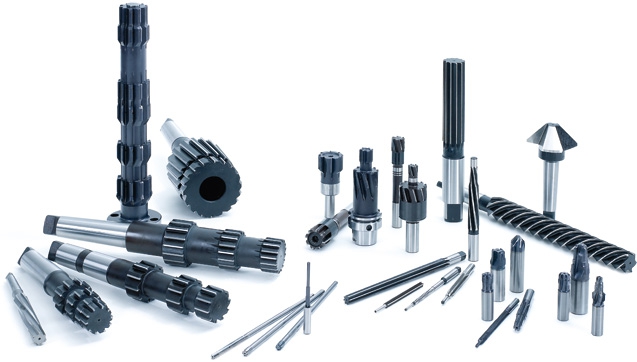
The continuing development of high-performance reamers together with the modern production facilities at BECK offer the best preconditions also for the creation of custom solutions. Starting from semi-standard versions with, for example, special fits, modified working lengths or modified cutting materials and cutting leads, the specialists at BECK can also design application-specific custom reamers. Multi-stage reamers, for example, offer further improvements in productivity and profitability.